Volga-Dnepr’s quick-thinking will help Canadian iron ore mining project increase its 2017 production
1 of 4 — Photo courtesy Volga-Dnepr Airlines2 of 4 — Photo courtesy Volga-Dnepr Airlines3 of 4 — Photo courtesy Volga-Dnepr Airlines4 of 4 — Photo cou
1 of 4 — Photo courtesy Volga-Dnepr Airlines
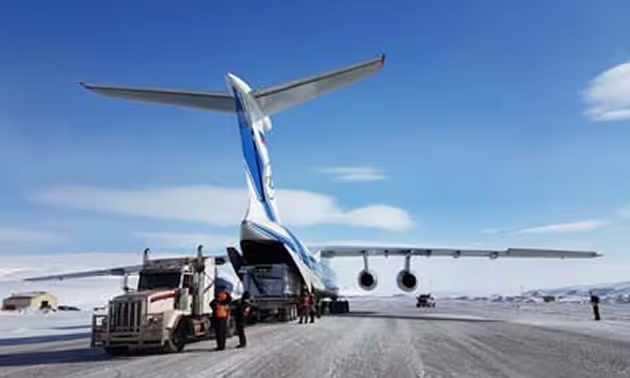
2 of 4 — Photo courtesy Volga-Dnepr Airlines
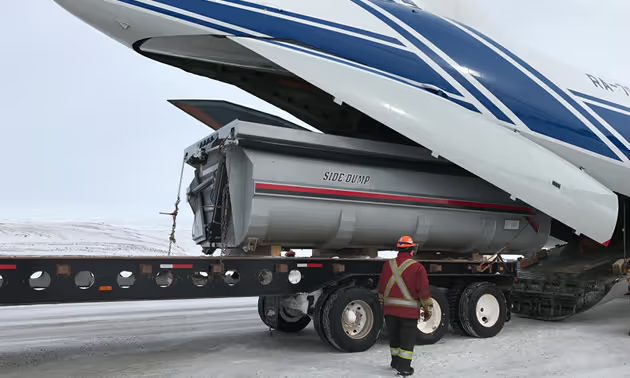
3 of 4 — Photo courtesy Volga-Dnepr Airlines
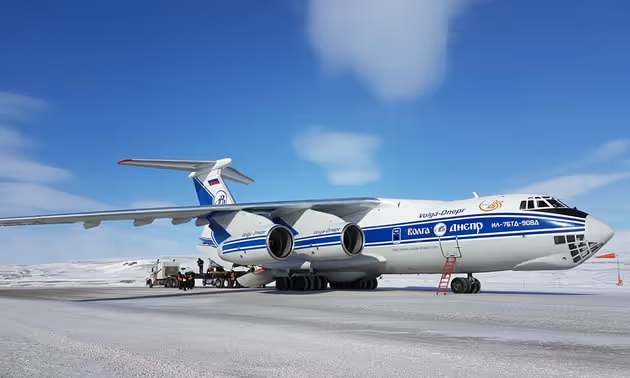
4 of 4 — Photo courtesy Volga-Dnepr Airlines
Volga-Dnepr Airlines’ outsize cargo specialists came up with an innovative solution to help the Canadian mining company Baffinland Iron Mines increase its iron ore production quota in 2017 at its Mary River operation in North Baffin, Nunavut, Canada.
In 2016, Baffinland achieved 3.2m tonnes of production and transportation of iron ore fr om the mine to the port site 100 km away. Much of the equipment already on the island arrived by sealift during the summer but with ice having shut down shipping lanes, no further deliveries would be possible until late July or early August. Recognising the need to increase the size of its truck and trailer fleet, Baffinland turned to Volga-Dnepr for its expertise in moving heavy and outsize cargo as well as the ability of its IL-76TD-90VD freighters to operate to Arctic runways.
In addition to increasing its fleet capacity, Baffinland needed the extra equipment because the extreme winter weather conditions and harsh ground environment were causing its existing equipment to need regular maintenance, thus reducing its availability. However, the trucks were too tall to fit inside the IL-76TD-90VD cargo cabin so Volga-Dnepr’s engineers set about finding a solution, working closely with the Baffinland team. With weather conditions of up to -50 degrees on site, plus the need for the new equipment to enter service quickly, it was essential to minimise the level of dismantling of the trucks in order to eliminate a lengthy re-assembly process on arrival.
Volga-Dnepr’s solution was to put smaller tyres on the tractor units for transportation, reducing their height sufficiently to fit inside the IL-76TD-90VD. Volga-Dnepr’s team also worked with Ilyushin Design Bureau to address the issue of the short 6,500 feet runway at Mary River and found a solution to use the least amount of fuel in order to safeguard the limited fuel supplies available on the island. Using the aircraft’s extension ramp equipment and onboard cranes also ensured the programme was self-sufficient in terms of loading and unloading.
With all of the planning completed, including gaining the necessary approvals from Transport Canada, Volga-Dnepr commenced a four-week programme of 20 flights at the start of April. This included positioning extra crew in Canada to ensure the timeliness of the flight operations for the four-hour rotation from North Bay to Mary River and back again.
Clair Gunn, Account Manager at Volga-Dnepr, who worked on the project with the airline’s specialists in London Stansted and Ulanovsk, said: “Weather systems can come in very quickly in Mary Island so you have to be prepared. Having extra crew availability meant we were able to meet our delivery schedule even though we had two days of blizzards and white-out conditions during the flying programme. We are proud to have delivered a solution that will make a significant contribution to Baffinland achieving their iron ore production quota this year.”
Baffinland Iron Mines’ Chief Procurement Officer, Sandeep Kumar, added: “We are quite delighted with the solution and service provided by Volga Dnepr’s team in response to our need for the mine. When we started the search for a solution, we were apprehensive of finding a workable and reliable solution in the short timeframe that we had ahead of us. It is to the credit of the Volga-Dnepr team, who provided us with commercial, technical and project management expertise through the process to come up with a detailed and reliable plan. The communication between Volga-Dnepr and BIM representatives as well as the third parties involved was smooth and effective, including the lead taken on permitting process. They understood the ground situation and worked accordingly. This gives us confidence of using such heavy airlift solutions should the need arise again.”