Newest diamonds for industry
3-D printed diamond is poised to revolutionize industrial tooling
Sandvik Additive Manufacturing presents a breakthrough for industry. — Photo courtesy Sandvik Synthetic diamond has been available for more than 60 y
Sandvik Additive Manufacturing presents a breakthrough for industry. — Photo courtesy Sandvik
Synthetic diamond has been available for more than 60 years, but its use in industry has been limited. Its extreme hardness—one of the properties that makes the material so useful—makes it less than amenable to being machined into the complex shapes needed in industry tooling. However, Sandvik Additive Manufacturing (Sandvik) of Sweden has now defeated that limitation with an exciting new process in additive manufacturing.
“Rather than looking to actually develop completely new materials, today the big push within the industry involves the often radical restructuring of existing materials,” said Annika Borgenstam, a professor at the Department of Materials Science and Engineering at Stockholm’s KTH Royal Institute of Technology.
“Using revolutionary new processes such as additive manufacturing will open up completely new ways of using the same types of materials that we have today, by building in the properties that we need.”
Sandvik has developed a diamond composite that has the potential to revolutionize the way industry uses the hardest natural material on the planet. The composite retains the most important physical properties of natural diamond, and can be 3-D printed into shapes to suit any industry’s need for tools and tooling systems—without the need for further machining.
“The additive manufacturing process used is highly advanced,” explained Mikael Schuisky, head of R&D and operations at Sandvik Additive Manufacturing. “We are printing in a slurry consisting of diamond powder and polymer using a method called stereolithography, where complex parts are produced, layer by layer, using ultraviolet light.”
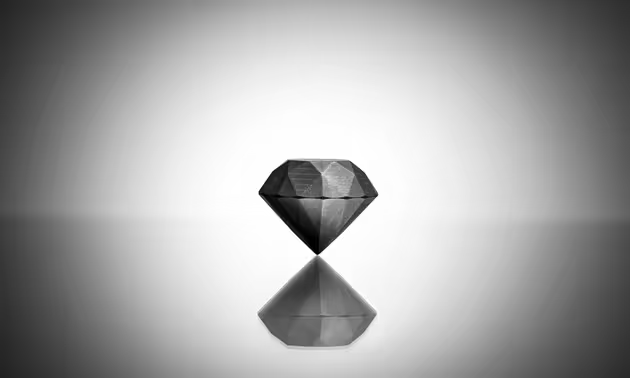
Sandvik Additive Manufacturing has developed a diamond composite that can be 3-D printed. — Photo courtesy Sandvik
Once the item has been 3-D printed from the composite, it undergoes specialized, proprietary post-processing to complete it. The leftover slurry can be separated, allowing the remaining diamond powder to be extracted and used again. This is a key economic and sustainability advantage of additive manufacturing.
The Sandvik website tells us that the printed composite is “three times stiffer than steel, with heat conductivity higher than copper, thermal expansion close to Invar—and with a density close to aluminium.” It is also highly resistant to corrosion.
Such properties mean that the composite can be used in advanced industrial applications that were previously considered impossible. It opens many possibilities for heavy industry, as well as medical implant manufacturing and space programs.
“Historically, 3-D printing in diamond was something that none of us imagined was achievable,” said Anders Ohlsson, delivery manager at Sandvik Additive Manufacturing. “Even now, we are just starting to grasp the possibilities and applications that this breakthrough could have.”
Sandvik unveiled its exciting new composite at the RAPID + TCT show—North America’s leading event for additive manufacturing—in Detroit May 21 to 23, 2019.