A secondary crusher comes to Copper Mountain Mine
This is the largest cone crusher to be installed in Western Canada
1 of 2The lower bowl frame of the secondary crusher in Kamloops, B.C., is waiting to be transported to Copper Mountain. — Photo courtesy Copper Mounta
1 of 2The lower bowl frame of the secondary crusher in Kamloops, B.C., is waiting to be transported to Copper Mountain. — Photo courtesy Copper Mountain
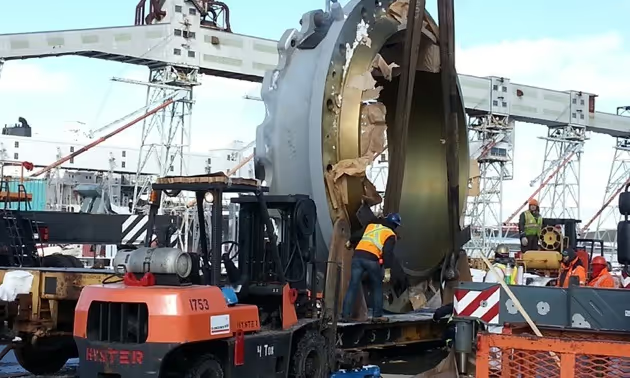
2 of 2The secondary crusher's upper main frame is unloaded at the Port of Halifax for transport via rail car to Kamloops, B.C. — Photo courtesy Copper Mountain
Copper Mountain Mining Corporation is installing a secondary crusher at its Copper Mountain Mine near Princeton in southern B.C. The machine, which will be the largest cone crusher in Western Canada, will replace three smaller, portable crushers that have been supplementing the mine's primary crusher.
The Copper Mountain Mine produces copper concentrate for smelters in Japan. Once the secondary crusher—a Raptor Cone Crusher manufactured by Denmark's FLSmidth—is operational by mid-2014, mine production is expected to increase to 35,000 tonnes per day.
Rod Shier, chief financial officer for Copper Mountain, said the secondary crusher will solve a problem that has been plaguing the mine since it was commissioned three years ago.
“The mine has not been able to consistently operate at design output levels (of 35,000 tonnes per day) due to the toughness of the ore,” Shier said. “The main bottleneck was in the SAG (semi-autogenous grinding) mill, which has had difficulty processing the larger pieces of ore. Installation of the secondary crusher will take care of this problem.”
Once the secondary crusher has been installed, ore from the mine will be put into the primary crusher, which will crush the rock into stones less than 5½ inches in diameter. The stones will then be transported by conveyor belt to the secondary crusher, where they will be reduced in size to less than two inches in diameter. After that, the ore will be conveyed to the SAG mill for further crushing and grinding.
“Installing the secondary crusher enables the ore to flow faster and more easily through the SAG mill, which will result in more copper concentrate production,” Shier said.
The secondary crusher is not just powerful but very, very big.
“When completed, it will stand 10 storeys high,” Shier said.
The lower main frame is the largest single piece of the machine. It weighs a little more than 100 tonnes and is almost six metres in diameter. It is so large, in fact, that it could not be handled by the Port of Vancouver. The equipment was shipped from Bucharest, Romania, to the Port of Halifax, where it was put on a train and taken to Kamloops. There, it was unloaded from its flat car by cranes and loaded onto a truck.
“Because of its size and weight, special permits and a special truck were required to move the equipment to the mine site,” Shier said.
It took four nights for Nickel Bros. Industrial Heavy Lifting & Moving to transport the equipment the 200 kilometres from Kamloops to the mine site, because the journey had to take place between midnight and five in the morning in order to minimize traffic disruptions along the route.
The equipment's slow journey to the mine site required a detailed traffic management program. First of all, the highway from the railyard to the mine site had to be blocked off in sections. Second, all of the bridges that the lumbering cavalcade crossed needed to be re-engineered to ensure they wouldn't buckle under the weight of the equipment. Finally, the convoy's progress was very slow; it travelled at a rate of only 10 kilometres per hour (an average person walks at a rate of six to seven kilometres per hour).
The total capital cost of the project is $40 million, which includes the cost of construction and the cost of the equipment.
“Construction of the secondary crusher is on schedule,” Shier said. “The major pieces have arrived on site and the foundation work is complete. The steel for the structure will be erected soon, and that will be followed by the new conveyor system's installation. We're scheduled to have the crusher operating by mid-summer 2014.”
The Copper Mountain Mine has a workforce of 420 employees and is located 20 kilometres south of Princeton. The mine produced 66.2 million pounds of copper in 2013. The 2014 production target is 80 to 90 million pounds of copper, plus gold and silver byproducts.
The mine is Copper Mountain Mining's flagship asset. The company has a 75/25 strategic alliance with Mitsubishi Materials Corporation. The mine began production in the summer of 2011. The 18,000-acre site has a resource of approximately five billion pounds of copper and remains open laterally and at depth.
“The mine has significant exploration potential that will need to be explored over the next few years to fully appreciate the property's full development potential,” Shier said.
The aim of future exploration is to define additional resources from numerous untested targets previously identified by a deep-penetration Titan 24 survey that was conducted in late 2007.