Remediating mine tailings and recovering gold
BacTech Environmental's first-of-its-kind bioleach facility at Snow Lake will remediate toxic mine tailings and process gold
1 of 4This photo from September 2010 shows the new Britannia Mine head frame, with ARS stockpile on the right and acid mine drainage in the forefront.
1 of 4This photo from September 2010 shows the new Britannia Mine head frame, with ARS stockpile on the right and acid mine drainage in the forefront. — Photo courtesy BacTech Environmental
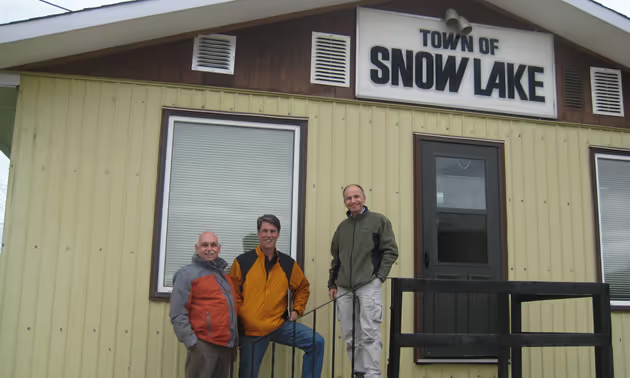
2 of 4BacTech visited the town of Snow Lake in September 2010. (L to R) Gary Williams, hydrogeologist; Ross Orr, president and CEO of BacTech; Paul Miller, VP of technology and engineering. — Photo courtesy BacTech Environmental
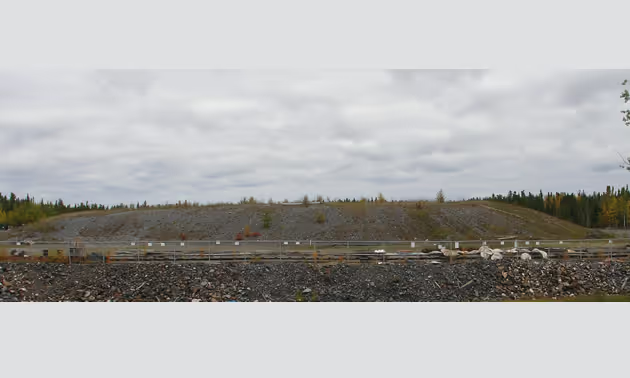
3 of 4This photo taken in September 2010 shows the 300,000-tonne arsenopyrite stockpile in Snow Lake. — Photo courtesy BacTech Environmental
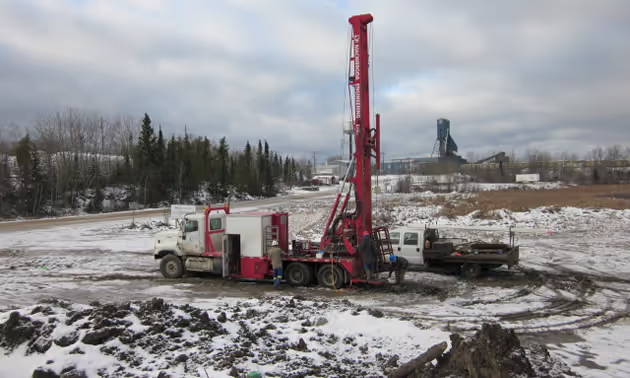
4 of 4Field investigation involving drilling deep test holes was done in November 2012 at the site of bioleach plant to be built by BacTech. — Photo courtesy BacTech Environmental
The first commercial bioleach facility in North America with the purpose of remediating toxic mine tailings will start construction this year in Manitoba.
The facility, being built by BacTech Environmental Corporation, is a $22-million plant that will process 100 tonnes of tailings per day on a 24-hour schedule for about seven years. The goal? To remediate the toxic mine tailings at no cost to taxpayers while seeing a profit from any gold the company can extract from the stockpile of arsenopyrite concentrate.
In December 2011, BacTech Environmental signed a contract with the Mines Branch of the Manitoba Department of Innovation, Energy and Mines to remediate the stockpile located in the community of Snow Lake in northern Manitoba.
BacTech is a pioneering environmental-technology company that has developed and commercialized a proprietary technology to remediate highly toxic tailings areas resulting from abandoned mining operations. BacTech's core technology, called bioleaching, employs naturally occurring bacteria—harmless to both humans and the environment—to oxidize the sulphide materials left behind after years of mining.
Ross Orr, president and CEO of BacTech Environmental, said it all started after he Googled "mine tailings” and “arsenic problems." His search led him to the Snow Lake mine site, which was operated by the Nor Acme Mine for 10 years and went broke in 1959. Based on an independent NI 43-101 report, the stockpile is estimated to be about 300,000 tonnes, with an average grade of around 9.7 grams per tonne of gold. The stockpile is six metres to 10 metres high and encompasses an approximate area of 19,500 square metres.
"The Snow Lake site is unique because it's already a concentrate," said Orr. "This pile has sat there for over 50 years and there are not so much streams but water areas coming out of the mine site that are bringing out a lot of acid—and with it, arsenic. This then goes into the Canada Creek and eventually ends up in Snow Lake, where the town gets its drinking water from."
Orr said with old projects like this, it falls into the hands of the government to clean it up, therefore costing the taxpayer. He said if a mining company disappears or goes bankrupt, someone has to step in. When Orr first went to speak with Minister of Mines Dave Chomiak—who had originally planned on just putting a cap on the tailings—Chomiak asked Orr what BacTech's plan was going to cost him. Orr told him it would cost him nothing as long as BacTech could get the gold extracted from the tailings.
"We call it the no-taxpayer approach," said Orr. "Why should the taxpayer pay for something that happened over 50 years ago—half of us weren't even alive. It's a unique model, that's for sure."
Since signing the contract with the government, BacTech has engaged the services of Micon International Limited to provide an independent economic study for the proposed reclamation. In August 2012, the study was completed and preliminary results released.
Orr said the patented Bacox bioleaching technology is applied to the processing of toxic, arsenic-laden mine tailings. An added benefit of bioleaching—in addition to stabilizing arsenic and capturing heavy metals—is that it oxidizes sulphides in mine tailings, thereby eliminating a major source of acid mine drainage. The technology also recovers precious and base metals from tailings for sale to market. Bioleaching is an environmental cleanup solution that also creates a profit.
So in simpler terms, because the pH of the bioleaching tanks is about 1.5—or very acidic—the arsenic and iron go into a solution and dissolve but the gold doesn't. At the end, you have a solid stream that has all the gold or silver in it and the liquid stream, which holds all the other stuff. Then, what you do is start raising the pH by adding limestone to the process, and the result is that the iron and arsenic bond together and drop out as a gypsum—basically that's your ferric arsenate.
Orr and his team have estimated that there is 92,000 ounces of gold in the Snow Lake stockpile. At today's prices, that equals about $130 million worth of gold. Production will see 11,000 ounces a year come out of the process, with BacTech receiving 95 per cent of the profit after the seven years is complete.
"This will be the first commercial bioleach facility in North America built to remediate toxic mine tailings," said Orr. "This is a major step forward for BacTech as we position ourselves as a leader in the field of tailings reclamation. It is a highly visible project whose success could lead to bioleaching playing a prominent role in future reclamations in North and South America."
For more information on BacTech and the Snow Lake project, or to see an informational video on the bioleaching process, visit BacTech's website.