New life for old technology
FLSmidth increases efficiency and minimizes environmental impact for clients.
FLSmidth is working on creating feasible, large-scale filtration systems. — Photo courtesy FLSmidth The Mining Suppliers Association of British Colum
FLSmidth is working on creating feasible, large-scale filtration systems. — Photo courtesy FLSmidth
The Mining Suppliers Association of British Columbia’s (MSABC) new mandates will include embracing innovative technology that minimizes waste, carbon footprints and the overall environmental impact of the mining industry. Most of their members’ goals align with this shift towards sustainability and optimized efficiency.
One example of an MSABC member working towards both environmental responsibility and operational efficiency is FLSmidth. FLSmidth engineers, manufactures, supplies and supports mineral processing equipment across British Columbia and globally. “Our success as a company is dependant on our clients’ success,” said John Davidson, Western Canada sales manager of FLSmidth and member of the MSABC executive committee. “Operating mines are looking to do more with less.”
Efficient mineral processing equipment
FLSmidth’s technology is especially useful in the mineral processing aspect of a mine. Once rocks are extracted from a mine, the largest cost and footprint factor is the significant energy costs associated with comminution—the breaking, crushing and milling of the rock. FLSmidth helps its clients optimize operating costs and implement efficient processes “so that the client can liberate the minerals from the rocks in the most cost-effective way possible.”
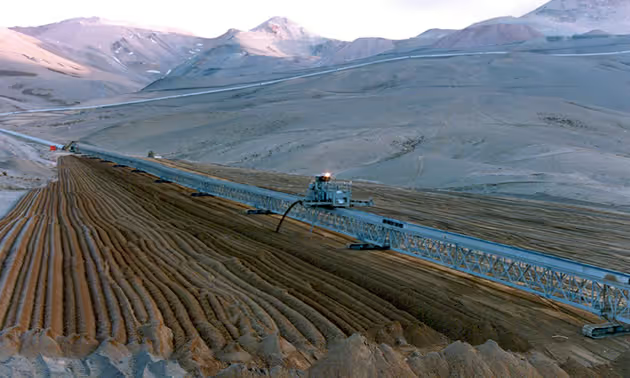
The mobile stacker deposits filtered tailings at the La Coipa mine in Chile. — Photo courtesy FLSmidth
One piece of technology FLSmidth offers is the High Pressure Grinding Roll (HPGR). HPGR technology is not new to FLSmidth, with numerous installations dating back to the mid 1980s in cement-based applications—their second area of expertise. HPGR technology has seen a steady increase in hard rock mining applications over the past decade. The trend will likely continue as the complexity and competency of ore bodies continue to increase. “A lot of the innovation is not necessarily new technology, just new applications of existing technology,” said Davidson.
Another cement-based technology FLSmidth is working into mining applications is the Vertical Roller Mill (VRM), energy-efficient alternatives to conventional SAG and ball mills. As is the case in HPGR, VRM is also a “dry comminution process” that reduces water consumption, as the VRM or the HPGR is not using electric energy to also move water with the rock. “How you use and deal with water becomes an environmental risk area,” said Davidson. “Mitigating your water use as best as possible not only results in significant cost savings, but also minimizes the total footprint or environmental risk potential.”
Although HPGR & VRM technology are considered “dry processes,” Todd Wisdom, global director of tailings solutions at FLSmidth notes, it does not completely eliminate the need for water. “When you do dry grinding, you still need water to do the separations of the minerals, so you can’t have a completely dry process at the moment,” said Wisdom. “The water that you use for separating what you want needs to be dealt with.”
Tailings management for large-scale operations
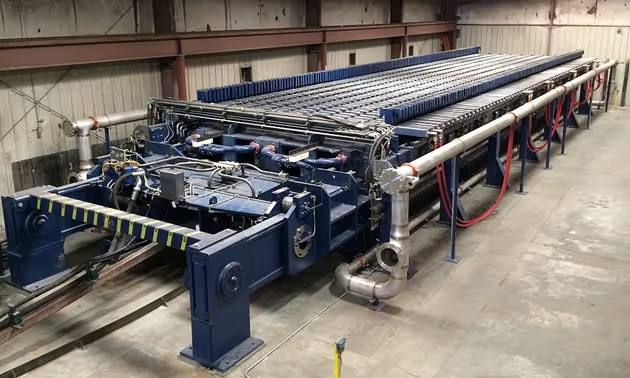
FLSmidth is demonstrating its large filter technology with hopes of having something for market by the end of the year. — Photo courtesy FLSmidth
Part of mineral processing in mining includes the leftover materials. The company has directed its current focus to tailings management. As a result of helping its clients optimize operational costs and risks surrounding tailings management, FLSmidth simultaneously helps these same clients minimize environmental risks.
For large-scale mines, conventional systems hold the danger of dam failure. “We see that there is the tailings risk. The big thing to understand about the risk is that it is not the dam failure that causes the damage, but the pool of water sitting above the dam that causes the damage.” Eliminating the pool of water minimizes the risk of harmful materials being pushed downstream.
The obvious solution is dry stacking tailings in a mine. Currently, while many mines use this technology, the costs associated with installing and operating filtration systems are not feasible for large-scale mines. FLSmidth is working on making feasible, larger filters. “We are trying to understand better the relationship of what is made at the concentrator when you dewater it, to how it conveys and how it’s placed and makes the Tailings Storage Facility (TSF),” said Wisdom. “We are looking at different flow sheets to try to optimize the cost and performance. Not only are we going bigger, but we are looking at new technologies.”
FLSmidth is already actively demonstrating its new tailings management technology with hopes to have something ready for the market by the end of the year. “There is a demonstration of a large new filter press at a large concentrator in Chile that is in startup commissioning right now. There are also other new technologies testing in Canada that should help considerably to reduce the OPEX of filtered tailings making it competitive with thickened tailings,” said Wisdom.
Environmental responsibility in British Columbia
“I think that our mining community specifically in British Columbia has a good track record of being good stewards of the environment,” Davidson said. “In other places in the world, you feel like community relations and environmental protection are much more secondary. That’s not the case in British Columbia.”
Especially with the implementation of the MSABC’s new mandates, this environmental stewardship can only improve. “My perception of my clients is that they spend a lot of time, effort and money proactively and effectively engaging with the community and environment,” said Davidson.
As mining becomes more challenging and environmental responsibility becomes a priority across the country, the industry will have to continue to improve. “The mining companies and suppliers have to continue to co-develop and invest in new technology both to lower capital and operating costs, but also to find new ways to deal with their revenue streams such as increased recoveries of the minerals they are processing,” said Davidson, “as well as dealing with tailings produced.” FLSmidth and other British Columbia suppliers are working to meet these needs.
“I think that our mining community specifically in British Columbia has a good track record of being good stewards of the environment,” Davidson said. “In other places in the world, you feel like community relations and environmental protection are much more secondary. That’s not the case in British Columbia.”
Especially with the implementation of the MSABC’s new mandates, this environmental stewardship can only improve. “My perception of my clients is that they spend a lot of time, effort and money proactively and effectively engaging with the community and environment,” said Davidson.
As mining becomes more challenging and environmental responsibility becomes a priority across the country, the industry will have to continue to improve. “The mining companies and suppliers have to continue to co-develop and invest in new technology both to lower capital and operating costs, but also to find new ways to deal with their revenue streams such as increased recoveries of the minerals they are processing,” said Davidson, “as well as dealing with tailings produced.” FLSmidth and other British Columbia suppliers are working to meet these needs.