Innovative technology takes on glacier climate and wins
FilterBoxx wastewater treatment technology overcomes the extreme climate of northern British Columbia
FilterBoxx's wastewater treatment plants use membrane bioreactor technology to meet environmental standards of water discharge at the mine site. — Pho
FilterBoxx's wastewater treatment plants use membrane bioreactor technology to meet environmental standards of water discharge at the mine site. — Photo courtesy FilterBoxx
An innovative wastewater treatment plant has overcome the challenges of a mining facility in the far northwest of British Columbia. This plant now sits atop Knipple Glacier, which is 65 kilometres north of Stewart, B.C., and receives the second largest amount of annual snowfall in Canada.
“What FilterBoxx did for this particular project is wastewater treatment as well as sludge dewatering,” said Renee Beaucage, sales manager with FilterBoxx. As one of B.C.’s largest mining companies, FilterBoxx’s client required an extremely innovative solution to manage the site's challenges including footprint limitations, extreme cold, record-setting snowfall and limited access to the site. The system was transported by a snowcat up the glacier.
“When we first started this project, we provided (our client) with a temporary wastewater treatment plant for their initial construction phase,” said Beaucage. This initial plant treated 75 cubic metres of wastewater each day, supporting about 300 people. From day one, the treatment facility met the Ministry of Environment's guidelines.
What makes this initial plant special is that it is a membrane bioreactor (MBR) plant. The MBR plant uses an ultrafiltration membrane in a suspended growth bioreactor. Solids are filtered out of the wastewater and retained in process tanks until further processing in an aerobic digester. These systems are entirely automated for remote access and easy operation.
All FilterBoxx treatment plants are pre-assembled, and fully functionally and electrically tested prior to delivery. This is especially critical for this project due to the challenging glacier site. “Because of the location, these were requirements for our client,” said Beaucage. The location of the mine also necessitated meeting strict discharge regulations.
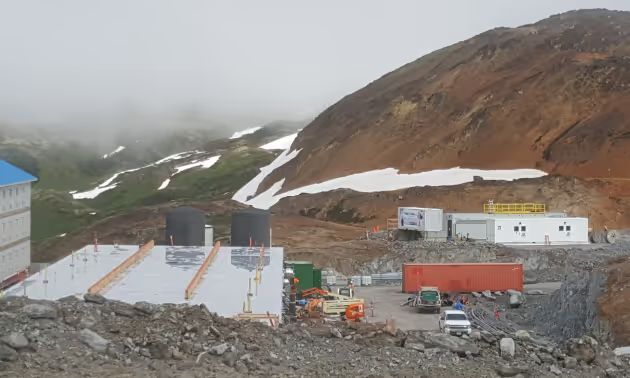
The MBR plants are automatic and easy to operate. FilterBoxx also has access to the system from anywhere in the world should their client require extra assistance. — Photo courtesy FilterBoxx
The client on Knipple Glacier also recruited FilterBoxx for its permanent camp upon completion of the mine site. “For their permanent camp of about 660 people, we were then asked to provide a system that would be adequate for that population,” said Beaucage. “We combined the temporary plant already on site with a new identical plant, so they would have two of the same treatment plants on site.” This allowed for a seamless integration as well as ease of operations and common spare parts.
The expanded facility supports 150 cubic metres of wastewater per day and also includes a sludge dewatering system to further reduce and prepare solid waste before on-site incineration. The sludge dewatering system meets all requirements necessary for the remote, glacier location. “It’s an integral step to the overall solids handling and disposal system for the camp,” said Beaucage. Again, this second plant as well as the sludge dewatering equipment will be tested and assembled prior to delivery at Knipple Glacier.
The two wastewater treatment plants and sludge dewatering equipment are contained in separate steel buildings which continue to stand up to the harsh climate found at Knipple Glacier. At times, the buildings are completely covered in dense snow. “An important part of this project is providing this type of robust system to withstand the harsh year-round winter conditions in this area,” said Beaucage.
FilterBoxx initially operated these systems but have since trained its client’s employees to create a self-sustained operation. However, FilterBoxx’s technology still allows for remote access and operation from anywhere across the globe should its client require extra assistance. “If they ever have any trouble on site, we can always tap into the system. We can monitor what is happening remotely and help operations,” said Beaucage. “We still support the client.”