Fabric structures used on massive hydroelectric project
Buildings were needed on location to service all the equipment and provide general warehousing of materials
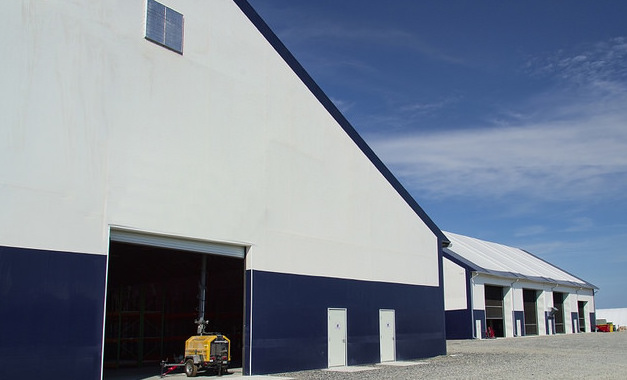
The fabric warehouse and maintenance buildings at Keeyask Generating Station were custom designed to meet project specs. — Photos courtesy of Legacy Building Solutions of Canada /Impact Photographic Design, Canada
When Manitoba Hydro, in conjunction with four Manitoba First Nations, put up the bid for its new Keeyask Generating Station on the lower Nelson River in northern Manitoba, a group of contracting companies recognized how formidable the task ahead would be and decided to form a joint venture. Bechtel, Barnard Construction and EllisDon converged to form BBE Hydro Constructors.
The team is responsible for constructing a seven-unit powerhouse, building 25 kilometres of earthen dam or dike structures, and excavating a significant amount of rock. The contract also calls for electrical and mechanical work, a concrete spillway, and construction and removal of temporary cofferdams.
Once completed, the generating station will provide 440 gigawatt-hours of hydroelectricity annually. It’s expected that the plant will begin generating power in 2019, with final completion slated for 2020.
A project of this magnitude requires a lot of manpower, and also a lot of equipment.
Furthermore, much like an isolated mining application or oil exploration operation, the site of the Keeyask Generating Station is in an extremely remote area, about 175 kilometres northeast of Thompson and 30 kilometres west of Gillam, Manitoba. The combination of the location and the need for numerous machines meant that BBE would need temporary maintenance and storage facilities right at the job site for the duration of the project.
“Given the climate in the area and the overall scope of the job, we knew we would need buildings on location to service all the equipment and to provide general warehousing of materials,” said John Lehman, a superintendent with BBE. “We solicited bids from building suppliers for two structures based on previous projects where similar sized equipment."
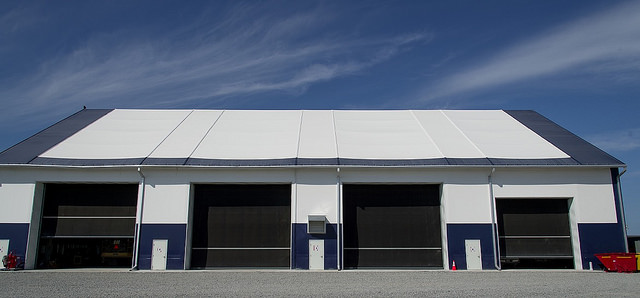
This building has rubber rolling doors on the sidewall. It’s fully insulated to protect equipment and machinery maintenance in the harsh winter conditions at Keeyask Generating Station. — Photos courtesy of Legacy Building Solutions of Canada /Impact Photographic Design, Canada
The specification parameters for the buildings included having enough room to accommodate large construction vehicles, as well as the space to operate a large crane inside. The most important criteria was that the building interior needed to be kept above freezing temperature at all times.
“We needed to have the buildings insulated,” said Lehman. “We have our in-floor heat and radiant heat inside, but the structures themselves required a certain R-value to maintain warmth in the winter months. A lot of the temporary structures in the region are fabric structures, so we mainly looked at those types of buildings, though we did consider a metal building as well.”
Legacy Building Solutions emerged with the most competitive bid and was selected by BBE to supply two fabric buildings to support the Keeyask station construction process. To meet the established environmental parameters, Legacy added R-30 insulation with a 7.5-ounce interior fabric liner to each structure to help combat the cold.
Like all Legacy fabric structures, the buildings were designed using the company’s innovative rigid-frame engineering concept, where structural steel I-beams are used instead of the open web truss framing historically found in the fabric building industry. Among the advantages of the solid beam design are straight sidewalls that maximize the usable space inside, and the capability to fully customize every aspect of the building plans.
The rigid steel frame for each BBE fabric building was finished with an oxide primer for enhanced corrosion protection. Outfitted to deal with potentially difficult weather conditions, the structures each feature three-foot overhangs with air flow in the soffit, along with icebreakers to prevent accidents or injury from snow and ice sliding off the roof. A gutter and downspout system was also added to both sides. Additionally, each building was rated to withstand 2.5 kPa ground snow load and 0.39 kPa windspeed.
The vehicle maintenance building, also known as the mechanic repair shop, measures 80 by 160 feet and is used for daily maintenance or periodic service on a wide variety of trucks and equipment. Machines at the larger end of the spectrum for the job include huge excavators and Cat 777 trucks for hauling rocks.
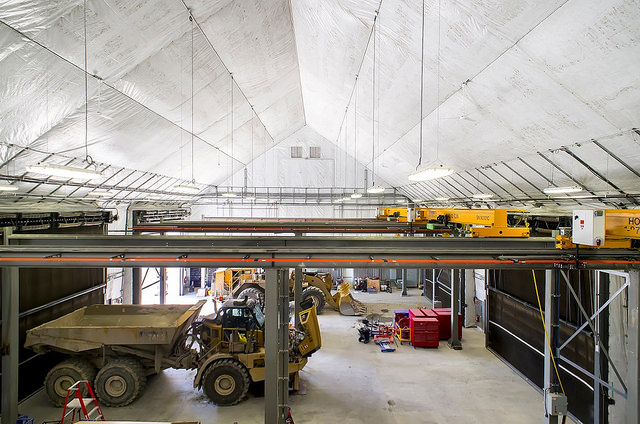
The maintenance building is big enough to accommodate a self-supporting crane along with lighting and heating equipment. — Photos courtesy of Legacy Building Solutions of Canada /Impact Photographic Design, Canada
To account for the vehicles and other equipment coming and going from the fabric structure, Legacy equipped the building with seven large TNR rubber roll-up doors. The building also has 12 insulated service doors providing access for personnel and small equipment. The durable roof and sidewalls of the vehicle repair shop are comprised of Nova-Shield 15-ounce, flame-retardant polyethylene fabric.
The second building, measuring 120 by 150 feet, is a warehouse holding materials and equipment to support the construction of the powerhouse and the dam structures. Along with vehicle parts and construction components, the building also contains lumber and scaffolding. Designed to provide ample room for shelving and forklift runways inside, the building’s ceiling height is over 18 feet high at the sidewalls, spanning to a peak clearance of 47 feet, 11 inches. The structure has a pier and curb foundation one foot above grade, and provides edge-of-dock, 25,000-pound load capacity levelers with a 78-inch plate, 15-inch bumpers, and a 27-inch mechanical flip leveler. Personnel and equipment can enter through seven insulated commercial steel coil doors or 10 insulated service doors.
“Due to the overall project timeline, the buildings had to be constructed in the dead of winter,” said Lehman. “So there were certainly environmental constraints with the extreme cold, but we were able to handle that challenge. Legacy sent a technical representative to assist the local crews, and the installation went well. We had a great working relationship with Legacy throughout the entire process. They supply a very high quality fabric structure, and we’re certainly pleased with what we’ve seen from the buildings thus far.”
Although the buildings were designed and constructed specifically for the Keeyask Generating Station project (just as BBE Hydro Constructors was formed for this single job) there’s always the possibility they’ll continue to be used in the future, either relocated for another job or put up for sale to another company. Since the buildings could be applied to virtually any industrial application, from mining to government to warehousing, chances are they’ll find a meaningful second life after Keeyask.
For now, BBE is just happy with the structures’ role in simplifying a few critical aspects of its massive operation. And in the often-complex world of energy production, anything that can come relatively easy is more than welcome.