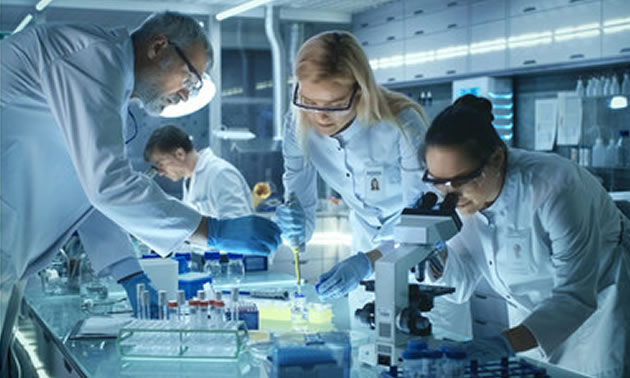
— Photo courtesy VanadiumCorp Resource Inc.
VanadiumCorp Resource Inc. (TSX-V: "VRB") (the "Company") is pleased to announce that it is publishing the results of Environmental Footprint and Energy Consumption Analysis and Comparison of The Vanadiumcorp-Electrochem jointly owned patent pending technology in addressing the recovery of vanadium from vanadiferous feedstocks. Furthermore, VanadiumCorp-Electrochem Process Technology combined with Electrochem Technologies & Materials Inc. ("Electrochem") patented iron electrowinning process focuses on the recovery and monetization of the iron metal values representing up to 65% of the feed in the particular case of titanomagnetite (VTM, magnetite) of various origins and in lesser extent the titania and silica values.
Adriaan Bakker, CEO of VanadiumCorp states, "85% of vanadium is derived from very few magnetite resources in the world with limited recovery, high cost and a large carbon foot print. Conversely, the new carbon free, high efficiency approach from VanadiumCorp-Electrochem represents maximum transformation of all value add products and vanadium electrolyte direct from ground source. The current mandate continues to assess global licensing opportunities representing potential cash flow and accelerated validation ahead of further patent and resource developments.
According to the World Steel Association in 2016, the worldwide steel production currently totals about 1.6 billion tonnes per year. The prevailing Blast furnace process produces pig iron from iron ore using carbon as reductant; the process releases carbon dioxide to the atmosphere. Production of a tonne of steel generates 1.8 tonnes of CO2 emissions, according to steel industry figures, accounting for as much as 5 percent of the world's total greenhouse-gas emissions. The industry has met little success in its search for carbon-free methods of manufacturing steel. Steelmaking is one of the world's leading industrial sources of greenhouse gases.
VanadiumCorp and Electrochem have developed a new chemical technology solution in early 2017 that can be both adapted and integrated into current steel and vanadium operations and constructed as a standalone facility to monetize all value add products of various feedstocks, carbon free energy, maximum recovery into high purity products.
Among the two conventional processing routes used industrially, only the smelting/slagging and roasting processes such as those formerly performed by Highveld in the republic of South Africa and New Zealand Steel in New Zealand were addressing the particular issue of full iron recovery. They did produce pig iron containing 1.25 mass percent vanadium first by smelting/slagging that was then converted into steel by injecting oxygen into the molten metal yielding a secondary vanadium-rich slag containing 12-24 mass percent V2O5 from which vanadium pentoxide was finally extracted by soda ash roasting and hot water leaching.
However, the energy consumed during the smelting and slagging steps together with the CO2 emissions are rather significant. To our knowledge no detailed life cycle analysis studies are available in the public domain regarding specifically the vanadium industry, however it is still possible to have access to reliable data regarding iron and steel making processes such as those published in: Fruehan, R.J.; , Fortoni, O.; Paxton, H.W.; and Brindle, R. (2000) - Theoretical Minimum Energies To Produce Steel for Selected Conditions. - Carnegie Mellon University, Pittsburgh, PA.
From the report, the actual specific energy consumption for producing a steel slab by smelting, steelmaking and hot rolling is on average 22.95 GJ per tonne of steel slab (6.380 MWh/tonne) while the GHGs emission is on average 1.8 tonne of CO2 per tonne of steel. This latter figure must be compared with 1 tonne of CO2 emitted during the production of one tonne of cement.
These numbers confirm the strong negative environmental impact of extracting vanadium pyrometallurgically using the iron and steelmaking route. These numbers do not take into account the specific energy consumption and CO2 emissions related to the soda ash roasting part of the process. In another report to the USGS [Bleiwas, D.I. (2011)] - Estimates of electricity requirements for the recovery of mineral commodities, with examples applied to sub-Saharan Africa. – US Geological Survey (USGS), Open-file Report 2011-1253, Reston, VA]: the specific electricity consumption for the production of vanadium pentoxide from pig iron is assessed as 3.000 MWh/tonne. This specific consumption was estimated based on limited data addressing the blowing of pig iron to produce vanadium pentoxide products and it includes crushing, grinding, and one or more of the following: roast-leach, rotary-kiln, electric-smelting, shaking-ladle, and basic-oxygen-furnace operations.
This should preclude implementation of new smelter capacities especially in jurisdictions where stringent environmental regulations were put in place as most governments agreed worldwide to reduce GHGs by implementing strict CO2 emissions reduction policies. Moreover, public acceptance towards implementing polluting technologies are at all time low while the trend is to promote green and cost-effective alternatives.
For all these reasons, integrating vertically the carbon and energy free VanadiumCorp-Electrochem chemical technology for vanadium, copperas, titania and silica recovery with Electrochem's patented electrochemical technology offers a unique competitive alternative to ironmaking by replacing the carbon reductant with electricity. Specific energy consumption during iron electrowinning can be as low as 2.900 MWh/tonne of electrolytic iron when operating under certain conditions (Canadian Patent CA 2,717,887 C) while the very low CO2 emissions would be linked to minor ancillary operations such as steam generation and drying. The various specific energy consumptions for each operation unit used in the integrated process are currently accounted from the flow sheet under assessment at the prototype level during Phase II. These data will be refined further during scale-up that will ensure more reliable data to be used as benchmark and for comparison purposes.
In conclusion, the two integrated technologies will be able to offer a highly cost effective and greener alternative to smelting and roasting in jurisdictions having access to affordable electricity either from hydro or nuclear power.
VanadiumCorp has a simple vision with global implications for many vanadium-titanium-iron resources, with a green process to benefit vanadium batteries for a sustainable future. To facilitate these objectives, the Company is developing new carbon free process technology with Electrochem in tandem with development of the Company's 100% owned, vanadium resources in Quebec Canada.