The Eastern Alberta Transmission Line (EATL) was energized in December 2015
The transmission line’s completion celebrates a generational investment for Albertans
The longest transmission line in Alberta’s history stretches from the southeast of the province to the Gibbons-Redwater area northeast of Edmonton. —
The longest transmission line in Alberta’s history stretches from the southeast of the province to the Gibbons-Redwater area northeast of Edmonton. — Photo courtesy Valard.
The longest transmission line in Alberta’s history, the Eastern Alberta Transmission Line (EATL), stretches 485 kilometres from Brooks in the southeast of the province to the Gibbons-Redwater area northeast of Edmonton.
In a news release issued by Atco Electric, the project’s owner and operator, company president Sett Policicchio said the transmission line’s completion celebrates a generational investment for Albertans.
“This transmission line will reinforce our electrical grid for decades,” he said in the release.
Valard completed all facets of the line’s construction from the foundations to tower assembly and erection, and stringing the conductors.
One of the main facets, starting with the assembly and erection of the towers, was putting together 1,387 heavy steel lattice towers using an internally developed assembly and erection procedure.
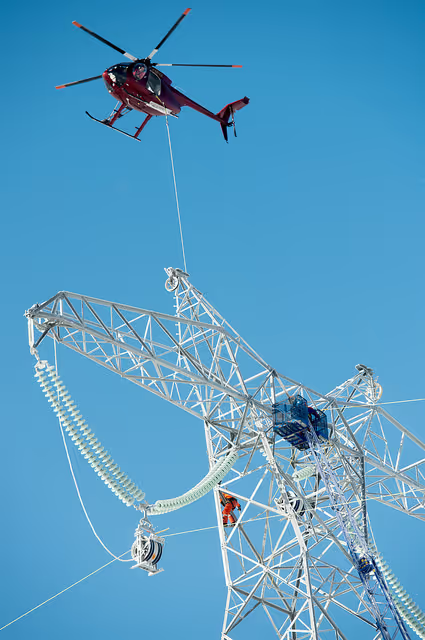
(EATL) Eastern Alberta Transmission Lines - Hanna — Mike Sturk photo
“We developed this procedure three years ago on a previous transmission line project for Atco Electric, where we assembled and erected these large lattice towers in one piece,” said Adam Borowiecki, project manager for Valard. “The crews would fully assemble the tower on the ground, and we would use two large cranes working together to erect them.”
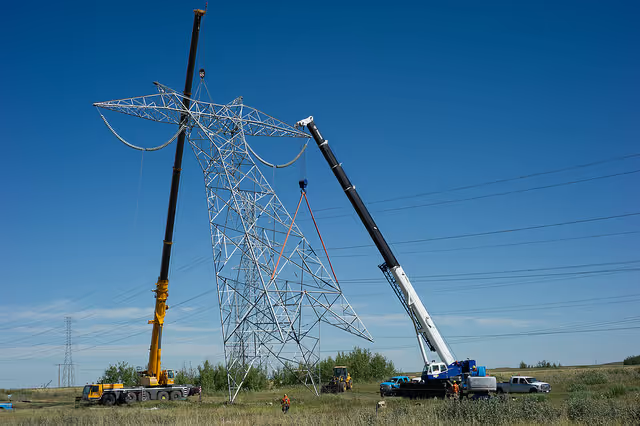
Atco Electric work Brooks - Hanna area. — Mike Sturk photo
“Traditionally, these towers were assembled and erected using a panelling and lacing technique, basically stick building them in the air,” he said. “Valard developed this new procedure to mitigate the safety risks with aerial work, as well as increase the efficiency of the work being performed.”
The company used helicopters as a key tool to string the 1,387 towers using a tension stringing method, which involves the helicopter pulling a bull rope through the towers—like threading a needle.
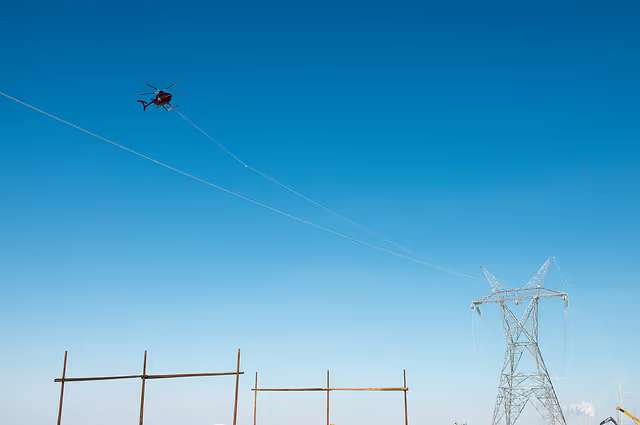
EATL) Eastern Alberta Transmission Lines - Hanna. — Mike Sturk photo
The helicopters fly approximately five kilometers through 15 spans of towers at a time, threading the rope through the dollies in the towers and connecting to the conductor at the other end. The crews utilized a large four-bundle 1590 conductor, and a “touch-and-go” procedure, where workers are flown to the tower, the helicopter hovers at the wing of the tower and workers step off of the helicopter’s skid and onto the wing of the tower.
“The entire project was an exciting challenge for Valard,” said Borowiecki. “We assembled and erected the two largest lattice towers in Atco Electric’s history, and installed the longest single-line fibre route as well.”
“EATL was a major milestone for Valard, as the transmission line work was fully completed by Quanta Services group of companies,” said Borowiecki, referring to Valard’s parent company as of 2010. “We didn’t outsource any of the foundation or transmission line work to other outside contractors.”
“Because the line is running the gamut from north-central Alberta to the south, the terrain and weather challenged the construction crews,” said Policicchio in an interview. “We get a lot of ice and heavy, wet snow in the south and cold snow that stays in the north so the terrain tended to be different on the foundations of each tower,” he said.
The foundations were designed after the soil work, and used a number of techniques including concrete piles in some places and anchors in other places. They run as much as 25 to 40 feet deep.
The other important aspect of the project for Atco was the extensive landowner consultation process.
“When we started the process we were working with about 10,000 landowners and ended up doing face-to-face consultations with 8,300 individuals, families and farmers to find a route that worked,” said Policicchio. “At the end of the day, we got it down to about 585 landowners we ended up dealing with and we were able to zero in on a site that was a fit for the majority.”
The project required just under 7,000 permits, including those for environmental considerations, and river, creek and road crossings.
“A part, too, we were building through winter on the rights-of-way and ended up using 70,000 rig mats,” he said.
At the time, EATL was Canada’s largest powerline under construction—Nalcor Energy’s current 1,200-kilometre project in Newfoundland and Labrador running 3,300 towers from Goose Bay to St. John’s surpasses EATL. Valard is also at work on the Nalcor project.
EATL’s labour requirement peaked at around 700 employees with significant emphasis on aboriginal workers and supporting aboriginal communities.
“We also had employees from coast to coast within Canada, the United States, as well as Europe,” said Borowiecki. “Our ability to utilize a global inter-company workforce was a major factor to the success of the project for us."
The new line reduces the amount of electricity lost during transmission, resulting in cost savings and reduced greenhouse gas emissions.
It is also expected to play an important role in the province’s Climate Leadership Plan by providing an essential infrastructure link for moving renewable energy, including wind and solar power, from where it is produced to where it is needed.
Immediately following testing and commissioning, EATL alleviated grid congestion for the Alberta Electric Service Operator by moving 300 megawatts of electricity from southern Alberta to the capital region.
Galloway Construction implemented an innovative mat washing system
Galloway Construction implemented an innovative mat washing system to meet the needs of the EATL, which used approximately 70,000 rigs mats throughout. With such an extensive right-of-way, the project’s focus and direction was dynamic, and rather than move lineally, all segments remained open along the span during peak construction. Weather, wildlife and landowner wishes called for a robust and dynamic working plan.
Galloway met the challenges by opening a regional field office with its own wash bay, and assigning a night shift to wash all project vehicles before the next shift. The company identified the need for and implemented Durabase mats to the project’s wood mat stock, and with so many to wash, developed automated tilt tables to ensure safety and efficient access to all sides of the wood mats.
Simultaneously, design and engineering began on a fully automated wood mat washing system – the world’s first – which operates as a closed system that allows a four-person staff to process 1,000 mats in a 10-hour shift, recycling all used water. This system, inspired by the EATL, will revolutionize mat management.
Galloway Construction implemented an innovative mat washing system to meet the needs of the EATL, which used approximately 70,000 rigs mats throughout. With such an extensive right-of-way, the project’s focus and direction was dynamic, and rather than move lineally, all segments remained open along the span during peak construction. Weather, wildlife and landowner wishes called for a robust and dynamic working plan.
Galloway met the challenges by opening a regional field office with its own wash bay, and assigning a night shift to wash all project vehicles before the next shift. The company identified the need for and implemented Durabase mats to the project’s wood mat stock, and with so many to wash, developed automated tilt tables to ensure safety and efficient access to all sides of the wood mats.
Simultaneously, design and engineering began on a fully automated wood mat washing system – the world’s first – which operates as a closed system that allows a four-person staff to process 1,000 mats in a 10-hour shift, recycling all used water. This system, inspired by the EATL, will revolutionize mat management.